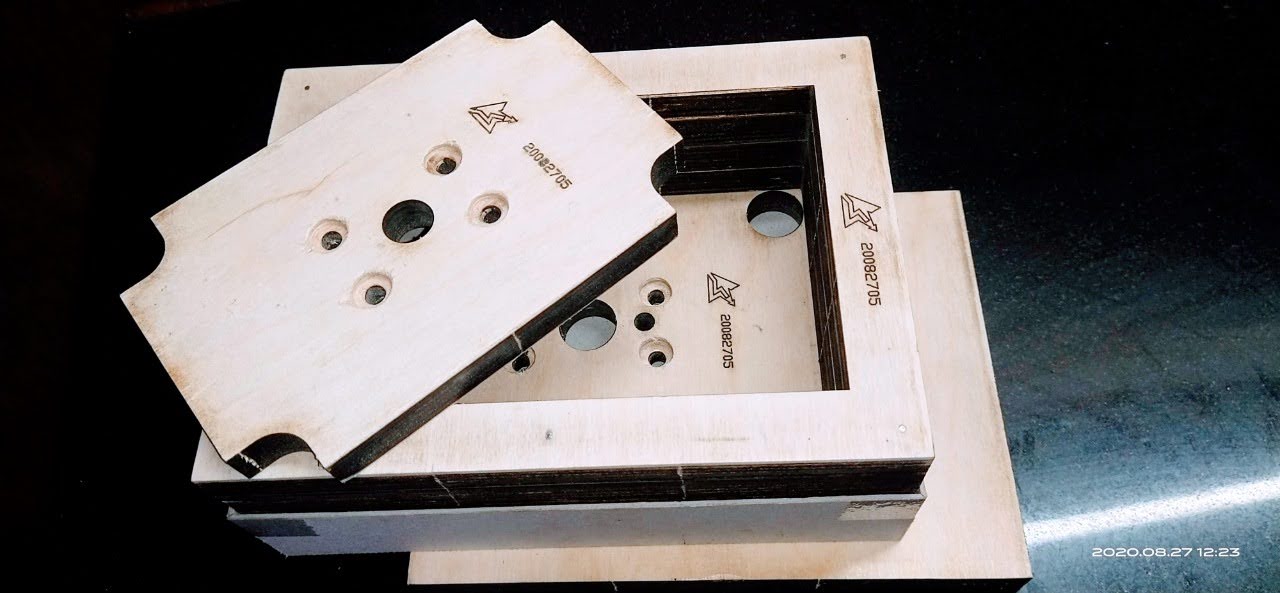
Keeping it simple, Die-cutting can be considered as a process of fabrication where materials like metals, wood, fabric, plastics, and other composites are converted into definite shapes and designs using specialized tools and machines. The process of Die-cutting can be done manually or automatically depending on the complexity and design requirements. The Die-cutting industry has evolved to a great extent and is applicable in various manufacturing industries right now such as packaging, household items, engineering equipment, electronic gadgets, office supplies. There are few industries that are left untouched by the process of Die-Cutting.
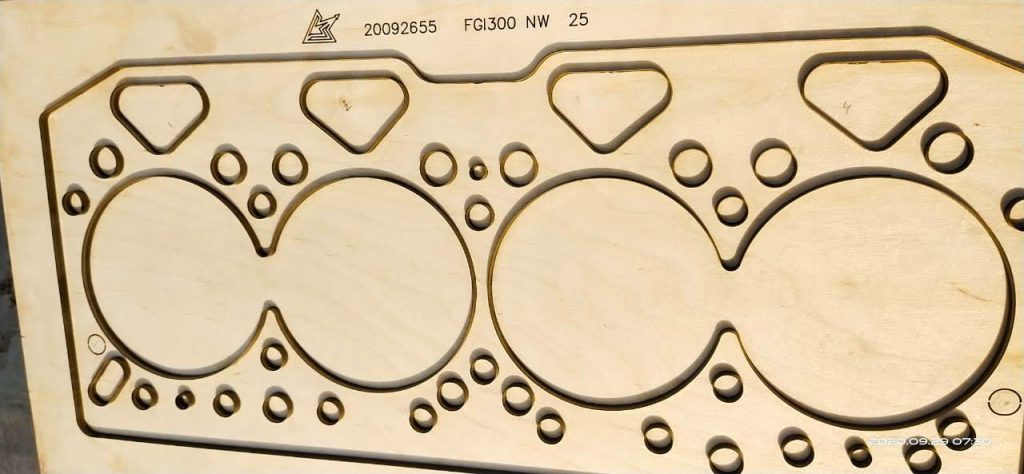
The history of Die-Cutting is entirely different from what it is now, this concept was introduced for cutting leather for the shoe-making process. This concept made it possible to manufacture shoes efficiently with more beautiful designs and perfection that was otherwise very difficult to achieve. It also promoted the mass production of shoes with less or no defects. With time, this amazing Die-Cutting process found its applications in many industries as discussed making it more versatile and flexible. As we can see advancements in technologies and machines, it is now possible to cut various elements like plastics, rubber, metals, foam, woods, etc. with ease and comfort. There is a production of unique, finished, accurate, and designer products when we make the best use of Die-Cutting tools and services. Not just efficient, this process is feasible, economical, and reliable making it the most preferred choice for all the cutting needs.
Since this process requires a great deal of perfection and efficiency, only skilled and expert professionals can handle this work. This ensures that the final product meets the specified standards and criteria.
Types of Die-Cutting-Tools & Machines
In the process of Die-Cutting, die-cut shapes are manufactured which are also termed as “blanks” which are then designed and integrated with other components or blanks to create the final object. This final product will now be used to cut the required material in bulk into fixed shapes and designs. This process involves the blades that are specially positioned and mounted on a strong background with a pre-designed form that can cut patterns, designs, and shapes into the material required. You can think of it as your favorite cookie-cutter but on an industrial scale. Coming to types of Die-Cutting, it is generally of three types: Flatbed Die-Cutting, Digital Die-Cutting, and Rotary Die-Cutting.
Flatbed Die-Cutting
This process is also known as steel rule die cutting, where blank or die-cut shapes are stamped with a flatbed die press and a customized steel rule die. The flatbed dies press can be of various models like electrical, mechanical, or hydraulic depending on the cutting application. The steel rule die cutting comprises a customized steel rule, a die base, cutting components of the die along with the component that holds the steel rule in a correct form and position. These steel rule die can also be of different types such as progressive, combination, progressive feed and blanking die.
We can use the flatbed Die-Cutting process when we want:
- To have an affordable and feasible cutting option
- To complete short production with a small number of orders
- To convert the material into sheets or rolls
- To process relatively thicker materials
- To manufacture larger parts
Digital Die-Cutting
It is a process in which materials are converted into desired shape and size without using dies, instead, it uses computer-controlled lasers, tool bits, knives, and blades to perform the task. These tools are suitable for producing designed and customized cuts, creases, and scores into the given material. The information or the design pattern is conveyed to the machine via digital signals and then it decodes it to produce the cuts and scores to create the final finished product.
We can use the Digital Die-Cutting process when we want:
- To process low-shear material along with high-shear materials
- To have higher precision and accuracy
- To reduce the lead time
Rotary Die-Cutting
In the process of rotary die-cutting, it comprises a rotary die press and customized cylindrical dies which rotate at higher speeds. This rotation of dies helps to cut the material into specific designs and patterns with more finishing and efficiency.
We can use the Rotary Die-Cutting process when we want:
- To process larger orders or productions
- To process thin materials
- To have higher accuracy
- Reduce waste production
- Designs have more tolerance
- Kiss-cutting process to be included
There is a lot that needs to be discovered in the context of die-cutting. With the evolution of technology, digital die-cutting is the emerging technology that will rule this industry in the near future along with maintaining peace with the other die-cutting methods.
Looking forward to exploring more about it?
Contact our team of professionals in case you need any assistance with die-cutting procedures and tools. We are taking every step forward to become the leading traders in the Die-Cutting Industry.